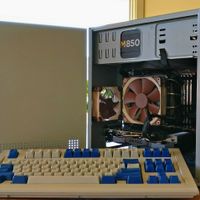
Guide
Projet PC Sleeper : la laideur a un nom
par Kevin Hofer
Une construction scratch est le rêve de nombreux passionnés de PC - c'est-à-dire que pour un PC, il ne suffit pas d'acheter les composants et de les monter, mais en plus de réaliser soi-même le boîtier. Deux apprentis de l'école professionnelle de Baden se sont lancés dans l'aventure et je les ai accompagnés.
"Demande d'interview" : c'est l'objet du message Outlook qui s'affiche sur mon bureau. Demande d'interview ? Je n'ai pas d'interviews ouvertes pour le moment. Quelqu'un s'intéresse-t-il à moi ? En effet, Viktor et David de l'école professionnelle de Baden veulent m'interviewer sur le casemodding. Je suis très honoré. Mais je me demande en même temps si je suis la bonne personne pour cela. Jusqu'à présent, mon seul projet d'envergure a été le Sleeper-PC.
Je leur explique que je n'ai pas beaucoup d'expérience dans le casemodding. Malgré cela, ils veulent faire l'interview avec moi. C'est presque une consécration.
La suite de l'échange par e-mail permet de comprendre l'objectif de ces deux personnes : elles doivent réaliser une interview en rapport avec le sujet pour leur travail d'approfondissement. Mais je trouve leur projet bien plus passionnant que l'interview avec moi : En tant qu'apprentis polymécaniciens, ils veulent utiliser leur savoir-faire pour construire leur propre boîtier de PC.
Quelques jours plus tard, je rencontre les deux ambitieux constructeurs de boîtiers de PC pour une interview. Viktor, qui se spécialise dans la construction, c'est-à-dire la conception de modèles CAO, me montre le projet de boîtier. Il l'a réalisé en collaboration avec David, qui s'occupe de la fabrication. Je réalise que je ne peux pas les laisser partir. Je veux savoir ce qu'il adviendra d'eux et de leur boîtier. Je leur propose que nous, chez digitec, fassions jouer nos relations avec Alphacool et leur organisions les composants pour le refroidissement par eau. En échange, je peux accompagner leur projet avec des articles.
Ils acceptent avec un sourire joyeux. Je passe du statut d'interviewé à celui d'intervieweur et interroge Viktor, le concepteur.
Comment vous est venue l'idée de créer votre propre boîtier ?
Viktor Weilenmann: L'idée est venue de David. Comme il est apprenti dans une entreprise de tôlerie, il a les machines nécessaires à sa disposition. J'avais pensé à faire quelque chose avec des PC pour mon travail d'approfondissement. Comme je travaille comme constructeur, je n'ai pas accès aux machines. Mais je voulais faire un travail qui me permette de fabriquer quelque chose.
J'ai trouvé l'idée de David très bonne. Je lui ai proposé d'utiliser mes compétences en CAO pour l'aider à concevoir le boîtier. Il se chargera ensuite de la fabrication.
Quelle était l'idée de base du design?
Nous avons d'abord esquissé quelques concepts et réfléchi à ce que nous pourrions fabriquer dans le temps limité du travail d'approfondissement. Nous avons décidé de fabriquer une tour midi.
Où avez-vous trouvé l'inspiration?
Nous avons parcouru des builds de PC sur Reddit et YouTube. Nous en sommes arrivés à la conclusion que nous allions refroidir notre système avec de l'eau. Il existe déjà de très bons cas. Je me suis inspiré de mon Define R6 de Fractal Design pour l'épaisseur des matériaux, la position des composants et les autres masses.
Qu'avez-vous fait en premier lieu ?
Avant de commencer officiellement le travail d'approfondissement, j'ai dessiné en gros un boîtier de PC. C'était une sorte de brainstorming directement dans la CAO. J'ai noté les éléments dont je devais tenir compte pour le projet proprement dit. Ensuite, David et moi avons fait un croquis et décidé de l'aspect approximatif de notre boîtier.
Comment avez-vous continué ?
Avec le concept et mes notes du premier design, j'ai commencé à créer le boîtier proprement dit dans Inventor Professional 2020 - un logiciel de CAO 3D.
Quelles ont été les difficultés rencontrées lors de la construction?
Le plus difficile a été de positionner la carte mère de manière à ce que le panneau d'E/S sur une tôle et les slots PCI-E sur l'autre s'emboîtent. Sur Internet, j'ai trouvé plusieurs sources de tailles de panneaux d'E/S qui ne correspondaient pas. J'ai donc décidé d'utiliser des modèles à l'échelle de Grabcad.com pour déterminer la position.
Nous avons également rencontré des difficultés avec le couvercle. Celui-ci doit couvrir les fentes des ventilateurs et laisser de la place pour un Infinity Mirror à l'avant. Nous ne savions pas comment visser le couvercle. Nous avons décidé de riveter des entretoises sur le panneau intérieur et d'y fixer un écrou à sertir. Ainsi, la position et l'espacement sont donnés. Nous avons utilisé des vis à tête moletée DIN 464 afin de réduire au maximum le risque d'endommager le panneau
.
Qu'est-ce qui a été particulièrement facile?
La découpe des ventilateurs sur la tôle et les pieds ont été faits rapidement.
Le montage du watercooling en CAO a également été facile, Alphacool mettant à disposition tous les modèles 3D de ses produits sur son site internet.
Vous prévoyez le dessous, le devant et le dessus d'une seule pièce de tôle. Quelle en est la raison ?
Nous voulons ainsi économiser des points de rivetage. Le rivetage nécessite ce que l'on appelle des languettes de tôle, au niveau desquelles les pièces de tôle sont rivetées entre elles. Cela n'a pas l'air très propre. Si nous fabriquons les trois pièces en une seule, nous obtiendrons des pliages propres sans rivets.
Quel est votre degré de satisfaction quant au design?
Je suis satisfait du boîtier. Cela a pris beaucoup de temps pour finaliser le design. La prochaine fois, je me concentrerais sur un boîtier plus petit, car je trouve les PC ITX petits et maniables très intéressants.
Combien de temps vous a-t-il fallu pour concevoir le boîtier ?
J'ai passé environ 60 heures, dont environ 8 heures pour les dessins de fabrication. Si je concevais un boîtier de A à Z, je serais certainement plus rapide. J'ai dû faire de nombreux ajustements pendant la conception. Avec les connaissances que j'ai acquises, je peux éviter certains problèmes dès le départ.
Alphacool contribue entre autres aux composants suivants :
Alphacool Laing DDC310 - Complete Edition Plaque de glace - noir/acétal
S'y ajoutent divers raccords.
Le boîtier final ne sera pas aussi coloré que dans l'animation. Les différentes pièces ne sont colorées que pour permettre à Viktor de les distinguer dans la CAO. Le boîtier doit être peint en noir, l'intérieur éclairé en blanc avec des tubes blancs et des raccords de couleur chrome. Sur l'Infinity Mirror, les garçons veulent faire briller une forme d'éclair. D'où le nom du boîtier : Zeus. David est un fan de la mythologie grecque.
La prochaine fois, je rendrai visite à David dans son entreprise d'apprentissage et je regarderai par-dessus son épaule pendant la fabrication de Zeus.
La technologie et la société me fascinent. Combiner les deux et les regarder sous différents angles est ma passion.