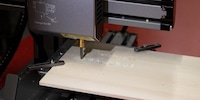
Product test
Milling, printing, engraving: Is the Snapmaker the all-in-one solution?
by Kevin Hofer
I have been bitten by the CNC bug. So I quickly ordered a kit from China. Was that a good idea?
My review of the Snapmaker made me fall in love with CNC milling. The possibilities with a CNC router are simply brilliant. You can do a lot with acrylic in particular. I'm thinking of making my own distro plates for the water cooling of my PC. Oh, how nice it would be to have my own milling machine.
I've never operated a machine like this before, and now I really want more. And when I'm desperate for more, I tend to make impulse purchases.
CNC stands for "Computerised Numerical Control" and refers to an electronic process for controlling machine tools.
A few weeks after my Snapmaker review, a cheap CNC kit from China is sitting on my desk at home. That's what I get for not being able to control my emotions. Anyway, I can now embark on my CNC adventure. After all, I like making things. If the thing is no good, I'll have fun putting it together - at least I hope so.
I set about screwing the part together. As soon as I look at the instructions, it's clear that they're no good because they're not detailed enough. Fortunately, other people have already assembled the kit and published complex video instructions on YouTube. Nevertheless, it took me over four hours to assemble it, but see for yourself.
Despite the great video instructions, I had a few problems during assembly. For example, I accidentally assembled the Z-axis carriage the wrong way round. Looking at the video, I don't understand how I could have done it wrong. It's obvious how it should be right. Embarrassing, embarrassing, I must have been too cerebral.
Now that the machine is assembled, I can finally start milling. I download the USB port driver and install it. This enables my PC to recognise the Arduino-compatible control board. To communicate with it, I download GRBL. GRBL is an open source software that can convert G-code and convert it directly into control commands for the CNC output stages. G-code is a machine language that I use to tell the CNC machine what to do. As soon as the software is installed, I connect my milling machine to the PC via USB cable. I can hardly wait to get started.
I open the programme and select the correct USB port. I should now be able to move the axes of the machine using the jog button. But nothing happens. I can see the axes moving on the GUI, but my milling machine remains still. What's going on?
After several hours of trial and error, I find the problem. For the second time, an embarrassment: I haven't fully plugged the power cable into the power supply. What a rookie mistake.
Never mind, now I can finally start milling - at least I think so. First I need a G-code. For my first attempt, I want to mill a lettering with "Test" and a circle. To do this, I create a sketch in Fusion 360, a 3D tool for CAD, CAM and CAE that is free for private users. Once I have finished the model, I have to generate the G-code. My experience with Fusion 360 is very limited and I have never converted my sketches to G-code.
I'm overwhelmed by all the setting options. Never mind, I think to myself, the default settings will be fine. I create the code. As I mainly want to mill acrylic, I clamp a three millimetre thick piece directly onto the building board. I don't use a sacrificial plate (base) for protection, as my test model will only be one millimetre deep. I create the zero points for all three axes and load the G-code into GRBL. Now I just have to press start.
The spindle starts to rotate and moves from the X/Y zero point to the milling start point. Everything seems fine until I suddenly hear a hell of a noise. If only I had screwed on a sacrificial plate. The router has drilled through the acrylic glass into the building panel. I pull out the mains plug and hope the machine isn't broken.
My settings must have been completely wrong. Not only were the Z-axis settings wrong, but also the speed of the router. The acrylic glass melted around the cutter. I can throw the part away. At least the machine still works. I can move the axes and the spindle is still functional. That would be the third embarrassment in my short CNC adventure.
I definitely need help. I find YouTube tutorials okay for software, but when it comes to physical work and relatively dangerous tasks like CNC milling, I prefer to get professional help. I sign up for a one-day CNC milling course. My CNC adventure continues. I'll tell you about the course next time.
From big data to big brother, Cyborgs to Sci-Fi. All aspects of technology and society fascinate me.