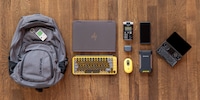
Background information
What’s in my bag: Martin’s keyboard isn’t a crowd-pleaser
by Martin Jud
During the «Keycap Kevin» focus week, I dedicated one episode to making a resin keycap – a so-called artisan keycap. Initially, a second episode was planned, but was scrapped in the end.
Did you notice anything strange going on in the artisan keycap episode of Keycap Kevin Week? In one shot during the conclusion, you see me holding a yellow resin keycap. In the next shot, the keycap’s dark.
So what’s the story? Between the two video shoots, I enjoyed a holiday in Corsica, produced several hours of video footage over two days and produced many failed attempts at making a decent artisan keycap.
After making my first DIY artisan keycap, I wanted more. That was back in early July of this year, when I was making one of these keycaps for an episode of Keycap Kevin. My partner in crime Thomas Kunz and I decided to produce a further episode on the artisans after my holidays in Corsica. How is the French Mediterranean island with its separatist tendencies relevant? Because it was on its beaches that I wanted to collect shells and sand to cast in resin. As I learned later, collecting neither of those things is actually permitted in France.
After my break, I returned to our studio in Zurich, carrying the following in my rucksack: illegally imported grains of sand and shells from Corsica as well as legally purchased resin. After my first successful attempt before my holidays, I was in good spirits as I got to work.
My plan was to immortalise the shells and sand in the resin in several casting steps. I realised 60 minutes into the curing process that it’s not as easy as I thought it would be.
The mould broke and my «shell in resin» project was a flop. To say I was disappointed would be an understatement. My face in the video speaks volumes.
But I can’t nor will I give up. So I decide to take a step back and give it a go with simpler keycaps. But in order for me to succeed, I need a new mould and a pressure vessel. The latter gets rid of any bubbles of air in the synthetic resin. The pressure compresses the air inside the resin to such an extent that it’s no longer visible to the bare eye.
Pressure vessels for casting resin are not only expensive but simply not available in Switzerland. My goal for the first episodes of Keycap Kevin was to achieve the best results on a small budget. I found out during my research that a colour pressure pot can be converted into a pressure pot for resin casting. It’s cheaper and seemed a reasonable solution to me. So I ordered one and converted it.
But in order to give casting artisan keycaps another go, I needed to make a new mould first. As with the synthetic resin, I used the Mold Start 30 by Smooth-on. By the way, I used the Smooth-Cast 326 for the resin. I went for those products because they were recommended to me by the Artisan Alliance. It was also with the help of their video tutorials and other tools that I made the mould and tried out the pressure pot for the first time.
Equipped with the new mould and the pressure vessel, I took the train to the studio in Zurich a few weeks later. Did I mention that I live in Biel and always transport all my stuff by train, bus and tram?
When I arrived at the studio that day, I had a feeling I probably wouldn't be able to make a keycap I’d be fully satisfied with. Why? Because my mould wasn’t perfect. I found this out after several trial runs at home. And yet, I was willing to give it a go while the camera was rolling. Be warned that this video, just like the two above, is a rough cut. So I take no responsibility if you get seasick. You can also see my failed attempts on the table.
Taking a look at the artisan keycaps after a bit of time has passed, I’d say they didn’t even turn out that bad. Sure, they have a few unsightly elements, such as stains and the imprints on the top caused by the template keycaps. But when they’re illuminated, those shortcomings are less noticeable.
Right at the end of the video clip above is when I’d draw my conclusion – that’s the one you saw in the episode on artisan key caps. And with it ends my odyssey with these ornate keycaps. At least for now. I do plan to keep experimenting and writing more articles about how I get on. In any case, I already have a new mould at home and also a few ideas to go with it.
The Keycap Kevin focus week was a success. Not least because of you, the Digitec Community. Thanks for contributing! There’s definitely a demand for content about self-made keyboards, and I want to cater for it.
Therefore, I’ll continue to pursue my project to make my own keyboard. And I’d appreciate any support you can offer. I’ll be needing your help for certain things. After all, I’ve never designed a PCB before, and I only have an enthusiast’s understanding of CAD. Also, I do want to make my own keyboard, but I want you to have a say in what direction I should be taking.
From big data to big brother, Cyborgs to Sci-Fi. All aspects of technology and society fascinate me.