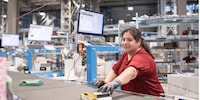
Behind the scenes
Update from Wohlen: most temporary logistics positions filled
by Mevlana Memeti
SonntagsBlick has denounced the working conditions at our logistics centre in Wohlen. The newspaper did so after speaking to half a dozen of our 800 logistics staff. We’ll be laying the truth of the matter out here in full transparency.
I’m conscious of the fact that not everything in our logistics centre in Wohlen always goes perfectly. In the last two pandemic years in particular, we’ve experienced a gigantic growth spurt, which has posed an enormous challenge for our employees and our business as a whole. During this period, we’ve hired hundreds of new logistics professionals. And we won’t deny that a few mistakes have been made in the process.
What saddens me is that the people quoted in the article don’t find our existing internal feedback channels sufficient enough to express their criticism. In addition to conversations with supervisors, managers or myself, I’m referring in particular to our regularly conducted staff surveys.
As a customer, you have a right to know what our working conditions are like. For full transparency, we’ll lay out the facts here. We’re happy to go into each of the key points addressed critically by the media, here:
«Customer satisfaction is the only thing that counts. There’s high pressure to perform and no consideration given to older and struggling employees» Customer satisfaction is certainly of enormous importance to us. Without high efficiency and quality, the competition would quickly sail ahead of us. But the satisfaction and health of our crew are just as important to us. We strongly believe that we can only achieve our ambitious goals with motivated and healthy employees. Our values build on this extensively. In every department, it goes without saying that we’re considerate of older and sick colleagues as well as those who care for relatives.
«Anyone failing to perform over several months is dismissed» Each and every employee, not just at Digitec Galaxus, has to deliver the performance they agreed to deliver. The same goes for a teacher, a carpenter or a care worker. They too are evaluated by their employer and can lose their job if their performance is insufficient.
If we notice that a colleague’s work isn’t up to scratch, we address the issue and look for solutions together. In extreme cases, we examine whether a change of role would be appropriate. If their performance remains unsatisfactory over a long period of time without there being a plausible reason behind it, a written warning is issued. This sets out what kind of improvements are expected from the employee. In addition, we set reasonable deadlines for the improvements to be made. Dismissing somebody from a permanent position is a last resort and only happens when their performance remains persistently unsatisfactory.
«Shift supervisors surveil and push their people» Shift supervisors ensure that operations run smoothly, organise work processes and support their people wherever needed. Our logistics centre in Wohlen is a co-ordinated production line. We can only handle our daily volume of orders, guarantee on-time delivery and ensure the highest possible standard of workplace safety if the number of employees working in each area corresponds with the numbers planned. It’s understandable that shift supervisors sometimes intervene when work is left undone. However, this must always be done respectfully and in accordance with our values. To guarantee this as far as possible, our managers receive continuous training.
«Monitoring via a traffic light system» The traffic light system in our receiving area isn’t displayed for all to see. Instead, the traffic light colours are discussed in monthly, one-to-one meetings between employees and managers. We think it’s important to give our employees regular feedback on different aspects of their work, including performance, quality and behaviour. When problems arise, improvement measures are discussed collaboratively. The content of these feedback discussions is confidential and isn’t communicated with other team members. In the past, concrete performance figures were given during these feedback discussions. The traffic light system (green/yellow/red) was developed and implemented in collaboration with employees as an alternative to that.
«Phone calls at work are not allowed» This isn’t the case. Employees in Wohlen are allowed to have their personal mobile phone on them at work. As is customary for all staff, calls should be restricted to breaks as far as possible. Urgent calls (to or from family members, for example) can, of course, be made during working time.
«Clock out for toilet breaks, smoke breaks or water breaks» All of our employees are entitled to their main breaks, as required by law. Anyone and everyone can go to the toilet or fill up their water bottle outside of these main breaks – obviously without clocking out. There are reasons why people working in logistics have to clock out when they take short breaks or cigarette breaks: each workstation has to be staffed as planned in order to avoid hold-ups in the downstream or upstream sectors of our facility. Our harmonised production line has to be kept up and running. Goods have to flow from the receiving area to the warehouse to the packaging area in a well co-ordinated way. We can only handle our daily volume of orders, guarantee punctual delivery and ensure the highest possible standard of workplace safety if the number of employees working in each area corresponds with the numbers planned.
«Six-day week, working weekends at short notice, impossible to plan family life» Our distribution centre in Wohlen is generally operational from Monday through Saturday – in other words, on six days of the week. Staff can be scheduled to work five days per week. If someone is scheduled to work Saturday, they’ll be off on a weekday. During busy periods, 6-day work weeks may be a reality. However, these are planned in advance and are well communicated. Each employee generally experiences this twice between October and December. Outside of peak times, an unplanned Saturday shift might also become necessary when the volume of work is higher than usual. Here, we rely on employees who voluntarily want to generate overtime they wish to take at a later stage. Employees who’ve built up a deficit of working hours due to personal reasons – and not because the company has mandated time off – are encouraged to make up these hours in a timely fashion. Any overtime can, of course, be compensated in full.
«In the pick tower, everyone has to run» The work carried out in the pick tower is physically intense. Our logistics professionals cover around 12 kilometres on foot during a working day – that’s about 1.5 kilometres an hour. So, nobody has to run to keep up with their workload. As mentioned in the introduction, we invited the journalist over on several occasions so that he could form a picture of what’s happening on site and speak to the people there. Unfortunately, he rejected our invitation.
«More performance per head» In actual fact, the revenue per employee, which was 3 million francs per full-time role when we were founded, has been continuously decreasing. In 2017, we reached our lowest figure to date of 1 million francs per full-time position. Since then, the figure has risen again slightly to 1.2 million per full-time position. These stats, however, aren’t particularly useful when applied to performance expectations for the logistics team. We have, after all, invested well over 100 million francs in the logistics facilities during this period. Today, our operations are automated to a large extent, which is why the figures are completely incomparable. However, we can’t allow productivity increases to be achieved at the expense of our employees. We’re becoming better by having our qualified workers make clever process improvements, optimise workstations and tools, and make operations more efficient via further steps in automation.
«Someone faints every few days» In each of the years 2020 and 2021, there were around 30 documented cases of nausea, circulatory or blood pressure problems at the Wohlen logistics centre. On each occasion, a company paramedic was in attendance. In total, around 100,000 workdays are completed in our logistics centre every year. That means that a member of staff suffers from nausea, circulatory or blood pressure problems once every ten years on average.
We take health-related incidents very seriously. Every case is one too many. Even if the figures are rather low for a logistics facility – in fact, no higher than the figures for our offices – our occupational health management specialists scrutinise every case. The fact that circulatory problems show up more frequently when people are doing physical work in the height of summer seems logical to us.
That’s why we’ve had measures in place to combat this for a while now. As well as aerating rooms and the use of a cooling unit, fans are provided at every workstation. In addition, there are plenty of water dispensers so that everybody can stay hydrated. We’re encouraged by the fact that the number of incidents has remained stable over the last few years, despite the number of staff doubling since 2020. That said, we’re working hard to optimise the working conditions in our logistics department.
«The company has no interest whatsoever in hiring permanent employees» This statement is demonstrably false. Since 2020, we’ve given permanent contracts to 400 temporary employees. That’s 55 per cent of all temporary workers hired during this period (722 in total). We would’ve liked to have taken on even more temps as permanent members of the team. It’s totally understandable, however, that they wanted to go back to their original professions once lockdown ended. In businesses like ours, which experience such strong seasonal fluctuations, deploying temporary workers is essential. In December, we have to contend with an order volume that’s twice as high as it is the rest of the year.
«Employees don’t trust the results of staff surveys» The internal staff survey – the «mood barometer» – is conducted anonymously three times per year, independently of any influence by managers. Employees can fill out the survey at work or on a private device. For Sonar, the comprehensive engagement survey, we offer logistics staff the option of filling out the survey at a specially set up workstation in a meeting room. In doing so, they can be supported by Personal and Organisational Development (POD) if they wish.
POD evaluates the results of the mood barometer. The Sonar survey, on the other hand, is analysed by an external partner. Managers subsequently receive completely anonymised reports. The comprehensive responses to these surveys help us to identify areas where action is required and to implement concrete improvements.
Overall, the results show that the logistics department isn’t doing badly by any means. In the last two years, satisfaction scores on the mood barometer, which are ranked on a scale of 1 to 10, have increased from just under 7 to 7.5. In the Sonar survey, our logistics department either achieved or surpassed the logistics norm both internationally (for logistics companies internationally) and in Switzerland (for Swiss companies across industries) in 9 out of 11 dimensions. In the remaining two dimensions, the logistics department missed the average figure by a few percentage points. These results show that the work atmosphere in the logistics centre is largely perceived as positive. We take the minority who don’t see it that way seriously and are grateful for their suggestions for improvement.
«Management’s leadership style is unacceptable» With such rapid growth during the pandemic years, we haven’t just doubled the number of employees in our logistics department within a very short time – we’ve also doubled the number of managers. Managers from very different corporate cultures, with varying levels of experience have joined us. And not everyone has been capable of behaving in line with our values. That’s why we’ve done intense work with new managers in order to familiarise them with our culture.
And that’s not going to change. We invest a lot of time and energy in leadership training and development. The ever-increasing satisfaction scores in our staff surveys, and day-to-day conversations with colleagues especially, show that this investment is paying off. We take insufficient social skills and misconduct very seriously. Unfortunately, we’ve had to part ways with some managers in the last few years, because despite training and clear guidelines, individual misconduct had occurred.
To all Digitec Galaxus colleagues, we, the management team, promise you: nobody who voices criticism, addresses grievances or makes suggestions for improvement has to fear any fallout. On the contrary, we need your commitment and feedback. Talk to us! This also applies to the colleagues who were in contact with SonntagsBlick. If we’re going to ease the pain, we first have to know where it hurts. My email address is florian.teuteberg@digitecgalaxus.ch.
My mission is to make shopping easier and better for customers and to offer my employees an inspiring working environment. I find a balance to work in a rowing boat or on a bike - although I usually travel there with my trailer and my children. Thanks to these, I am now able to enjoy LEGO and remote-controlled cars again. The time to give my PC once again a decent graphics card and to gamble through the night, I'm still looking for...