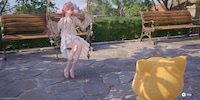
Background information
Where dress up and open world meet: Infinity Nikki
by Kevin Hofer
Kevin Buck has invested thousands of hours in his dream – designing a desktop CNC milling machine capable of working on metal. With the Kubus Pro, he now owns a unique device.
Kevin Buck’s showroom is located in an inconspicuous Aargau street. I say inconspicuous because a plumber uses the front area for storage. «At the moment, I can only use the rear section. But soon I’ll be able to take over the front too,» he says proudly.
Kevin recently started pre-selling his specially designed CNC milling machine. «I’m closing a gap in the market with my milling machine. It’s aimed at makers looking for a desktop CNC machine that can also mill metal.» With these words, Kevin persuaded me to visit his showroom a few weeks ago.
Once in his realm, he shows me what he’s spent many hours working on: the Kubus Pro. He has three versions on display – all prototypes. «I’m still waiting on a part for the latest one». All part of the process. Kevin has continuously improved his desktop milling machine.
Kevin has brought out his three prototypes, as well as various versions of the control unit, spindle, etc. He starts talking right away. Every part of his machine has a story. Take the cooling element of the stepper motor. «I tried out several designs. In the end, I opted for one with slits, in red. It looks really cool!»
Still, coolness isn’t everything. Kevin knows that too. He put all his know-how into the Kubus Pro. «Even as a child, I was fascinated by appliances and taking them apart.» After training as an automation engineer then studying electrical engineering, he worked as an electrical planner. However, he acquired most of his know-how for the Kubus Pro through self-study.
Kevin got into CNC milling through a previous hobby. «I was active in model making for a long time. I made spare parts using my first milling machine, especially for my aeroplanes. As the model flying community in Switzerland was small, I spent a lot of time using quadcopters. They flew so wildly that my planes were repeatedly damaged and I was often able to use my milling machine.» That was eight years ago. At the time, he had a GoCNC milling machine. It was delicate and only suitable for plastic and wood. He had to give up milling for a few years due to a move, which meant less space.
During the pandemic, Kevin wanted to start milling again. In his search for an affordable desktop machine, he realised that the market in Europe had dried up. «I asked myself: why shouldn’t I fill this gap? I then decided to become self-employed part-time.» In the beginning, he imported machines from China based on open build systems, adapting and developing them in his own way. «In the beginning, I did everything from home. My office and later my home gym became a warehouse. It eventually became too cramped for me and I rented a room here.»
Thanks to this extra space, Kevin was able to manufacture parts for his machines himself. He’s gradually made them more stable and improved them. «I wanted to make the machines more Swiss, so I used more parts from the Swiss value chain.» He achieved this step by step. In the case of the aluminium profiles for example, the bases for his milling machines, he first made the move from Asia to Europe.
But that wasn’t enough for Kevin. He decided to design his own milling machines – the idea for Kubus was born. That was two years ago. Initially, he planned to offer two models – a small one suitable for wood and plastic and a larger one for metal. «I quickly realised I couldn’t meet my quality standards that way. The little machine was always missing something. So, I decided to merge the two models.» The Kubus Pro can do everything the larger model could, it’s just slightly smaller.
This way, Kevin also found his niche in the market. «No one in Europe builds a machine like this for less than 10,000 francs. It’s the most powerful desktop milling machine in its class.» In this case, powerful means: a 500-watt spindle with a speed of up to 18,000 revolutions per minute. Class in this case means fully enclosed and between 3,000 and 7,000 francs. The spindle can be used to mill metal without any problems. «With a 3D printer, anyone can now produce parts in a very short time. They just aren’t particularly robust. This is where Kubus Pro comes into play.» The machine is also aimed at makers with higher demands. He’s also reached his goal of having as much Swissness as possible in his machine: over 60 per cent of the Kubus Pro’s value chain comes from Switzerland.
Kevin explains that aluminium can be milled in two ways: very slowly by removing little material or very quickly by removing a lot. There’s no middle ground, otherwise the tool will be damaged. «You can go full throttle with the Kubus Pro. It can easily achieve feed rates of three metres per minute for aluminium. No competing product can do that. Those only manage a maximum of one metre per minute with less depth adjustment.»
Most of that competition comes from the USA or China. However, they’re all less stable and weaker. Still, at least the one from China has a tool changer. However, Kevin deliberately dispenses with gimmicks in the Kubus Pro. «Machines with lots of gimmicks need constant firmware updates. I don’t want that. There’ll never be an update to the Kubus Pro’s control system. It runs as it should right from the start, without any gimmicks.»
Kevin uses high-quality materials to ensure the machine runs as it should. Originally, he wanted to build the Kubus Pro on aluminium profiles. «They’re cheap and uncomplicated, but not always straight.» Since precision is important when milling, he relies on 5083 precision cast aluminium plates that are face-milled on both sides. «Sounds complicated, but that’s what they’re called.» Linear rails and ball screws are mounted on them.
He also deviated from his original idea with the wooden side panels. Originally, he started out with medium-density fibreboard (MDF). «But it looked horrible.» So, he switched to oak. But carpenters advised him against it, as oak tends to warp and isn’t waterproof. That’s why he now uses multilayered bamboo for the Kubus Pro.
These adjustments were all relatively simple, as Kevin says. The biggest challenge for him was the circuit board design, he’d never done anything like it before. He drew the circuit board in the KiCad software. «Even with version one, I was confident it’d work and ordered several units. But the firmware wouldn’t run because I forgot a circuit board.» He wasn’t satisfied with the next few versions either. It wasn’t that they didn’t work, Kevin was just striving for perfection. «I’ve optimised the circuit board until it’s exactly the way I want it to be. One of a kind. No one else uses a physical safety relay and a hardware-based emergency shutdown.»
Kevin is just as proud of the spindle as he is of the controls. «Designing it was a massive undertaking. I’d never done mechanical engineering before. Bearing and concentricity tolerances are incredibly important.» He sought advice from engineer friends, but designed everything himself.
Now it’s time for Kevin to make sure the Kubus Pro passes standards tests. «I’m confident it’ll work straight away. I was always in contact with experts and did everything according to their specifications.» The tests are due in the coming weeks. As soon as he passes them, he can order the necessary parts. Quotes have already been secured.
It took two years for Kevin to be satisfied with everything. That equates to thousands of working hours. In the beginning, he even juggled his day job and self-employment. Now the Kubus Pro is on presale and Kevin works 100 per cent for himself. «It’d be great if I could sell even more in advance. I just don’t want to get too big, I can only build a maximum of ten per month on my own. If I sell two or three a month, I can make a living from them.» He’s also building an active community around the machine, setting up a Discord server for this purpose. He regularly posts videos and photos of his machines on Instagram.
Kevin is currently focusing on his own creations. In addition to the Kubus Pro, this also includes the Nexa Pro and Triton Next.
From big data to big brother, Cyborgs to Sci-Fi. All aspects of technology and society fascinate me.