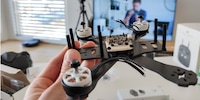
Retroscena
Il mio drone numero uno va in fumo, o quasi
di Manuel Wenk
Devo stampare in 3D un supporto per il drone da corsa fai da te del mio collega Manuel. Non è facile, perché possiamo comunicare solo digitalmente. Gli errori sono programmati.
La costruzione del suo drone da corsa ha avuto un inizio difficile per Manuel. Dopo poco tempo, ha dato fuoco al pezzo. E ora deve affrontare il problema successivo: la telecamera e le antenne hanno bisogno di un supporto, altrimenti non possono essere fissate. Un supporto che non si può comprare, ma che si deve costruire da soli.
Per fortuna ho la stampante 3D PlaySmart di Polaroid da testare - la mia stampante privata è di nuovo in riparazione. Manuel e io cerchiamo insieme i pezzi adatti su Thingiverse. Dopo un po' di tempo, pensiamo di aver trovato i supporti giusti. Utilizziamo questa parte per la fotocamera e questa per le antenne. Stampo i pezzi e glieli invio per posta.
Il supporto della videocamera si adatta, ma Manuel deve forare un po' i fori. Il supporto per l'antenna, invece, non si adatta. La distanza tra le due viti di fissaggio non è sufficiente. Non può avvitare il pezzo. Dobbiamo inventarci qualcos'altro. Propongo a Manuel di progettare il pezzo su misura utilizzando CAD e di stamparlo. Inizia un tira e molla con la comunicazione digitale del buon vecchio ufficio postale.
Ci incontriamo per una conferenza Teams. Questa volta facciamo tutto bene fin dall'inizio, o almeno così pensiamo. Discutiamo di ciò che Manuel deve misurare affinché io abbia le dimensioni corrette per il mio programma CAD Fusion 360. Anche se la staffa non è particolarmente complessa, sarà una sfida per me. Finora ho progettato solo cose molto semplici.
Abbiamo basato il progetto della staffa sul modello di Thingiverse, che però non andava bene. Un'altra cosa che Manuel ha notato è che i tubi per le antenne sono troppo lunghi. Dovrebbero essere più corti in modo che i cavi dell'antenna siano abbastanza lunghi da collegarli al cervello del quadcopter. Con le dimensioni corrette, mi metterò al lavoro.
La cosa più difficile per me è costruire il tubo dell'antenna inferiore con un angolo di 60 gradi rispetto all'antenna superiore. Non ho mai fatto nulla di simile prima d'ora. Ci riesco, ma la sezione trasversale del tubo passa da un cerchio a un'ellisse. In questo caso non è un problema: il foro nel tubo è ancora abbastanza largo da permettere a Manuel di far passare i cavi dell'antenna. Dopo circa quattro ore di lavoro, ho finito. Gli invio il progetto via Teams e ne discutiamo di nuovo in videoconferenza.
Guarda il mio progetto come modello 3D sul PC e lo confronta con il pezzo che ho già stampato per lui. Si accorge di una cosa: La staffa dell'antenna, che punta verso l'alto, si scontra con il telaio del quadcopter. Non può usare la staffa in questo modo. Sul suo quadcopter, un supporto per l'antenna deve essere rivolto in avanti e uno verso il basso.
Devo tornare ai libri. Affinché la staffa sia compatibile, entrambi i supporti dell'antenna devono uscire verso la parte anteriore. Quello che prima non era un problema, ora lo sta diventando: poiché la staffa superiore è rivolta in avanti e non più verso l'alto, devo orientare l'angolo della staffa inferiore verso il basso. Questo rende il cilindro ellittico estremamente stretto. È possibile costruire solo un piccolo foro attraverso il quale devono passare i cavi dell'antenna. Non siamo sicuri che i cavi ci passino. Spingo le dimensioni delle pareti al limite e le rendo estremamente sottili. Decidiamo di stampare il pezzo in questo modo.
Abbiamo spinto i confini di ciò che è possibile fare con la stampante 3D: Durante la stampa si sono formate delle crepe sui lati esterni del tubo ellittico. Il pezzo sta ancora reggendo e lo sto inviando a Manuel per posta.
Il problema con il tubo ellittico si è formato durante la stampa.
Il problema del tubo ellittico non mi dà pace. Non può essere che non ci siano altre opzioni. Visto che comunque ho dimenticato di salvare il mio progetto...
. Mi siedo di nuovo a Fusion 360. Quattro ore di lavoro per niente. Non mi lascio abbattere e, grazie all'esperienza del giorno precedente, la parte viene ricostruita in poco tempo, questa volta anche meglio. Scopro una funzione che mi permette di creare il cilindro in forma cilindrica. Stampo il pezzo e lo invio per posta.
Manuel cerca di inserire la staffa. Diverse cose non vanno bene. Innanzitutto, la distanza tra i fori per il fissaggio al quadcopter è troppo grande. Dovrebbe forare di nuovo. In secondo luogo, i tubi dell'antenna sono ancora troppo lunghi. Non è possibile collegare i cavi al cervello del drone. In terzo luogo, le protuberanze delle teste delle antenne, dove si trovano le unità di trasmissione e ricezione, sono troppo profonde. Le teste scompaiono completamente all'interno, cosa che non dovrebbero fare. In quarto luogo, ha misurato l'altezza della staffa in modo errato. Deve essere più corta di un centimetro. Devo rivedere il modello di nuovo.
Le regolazioni sono state fatte rapidamente e dato che il mio CR-10S Pro è ora di nuovo in funzione, stampo il pezzo con la mia stampante. Un nuovo pacco viene spedito per posta. Ora conosco a memoria l'indirizzo di Manuel.
"Anche questo!" mi scrive Manuel su WhatsApp. Merda, cosa c'è che non va ora? Poco dopo segue una foto.
Hmm... I cavi dell'antenna si adattano. Qual è il problema? La spiegazione: ha dovuto piegare il cavo per collegarlo in modo tale che il connettore si è rotto. Tutto il resto è a posto con la parte stampata. Si adatta perfettamente.
Discutiamo brevemente della situazione via Teams. Lui ordina delle nuove antenne e io rifaccio il pezzo. Questa volta allargo l'uscita per i cavi e la arrotondo. In questo modo è più facile guidare i cavi dell'antenna.
Il mio lavoro è terminato e lo sono anch'io. La prototipazione a distanza e senza esperienza è davvero noiosa. Tuttavia, sono orgoglioso che il pezzo sia finalmente adatto e che io abbia potuto aiutare Manuel.
Tecnologia e società mi affascinano. Combinarle entrambe e osservarle da punti di vista differenti sono la mia passione.