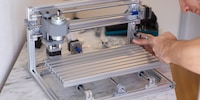
Hintergrund
Mein CNC-Abenteuer: Ein Scheitern in drei Akten
von Kevin Hofer
Meine ersten Schritte mit der eigenen CNC-Fräse waren alles andere als erfolgreich. Ich hole mir in einem Kurs Hilfe.
Samstagmorgen, elf Uhr, im Fab Lab Zürich. Ich und fünf weitere Teilnehmer schauen gebannt der CNC-Fräse zu, wie sie eine Halbkugel fräst. Als Laie macht es mir enorm Spass, einer so grossen Maschine zuzuschauen. Ich bin aber nicht zum Zuschauen hier, sondern für einen Fräs-Kurs.
Zur Erinnerung: Am Kurs nehme ich teil, weil ich bei meinem ersten Versuch in die Bauplatte gefräst habe.
Ein Fab Lab ist eine offene Werkstatt. Hier erhältst du als Privatperson Zugang zu modernen industriellen Produktionsmitteln. In der Schweiz gibt es bereits einige Fab Labs, und es werden immer mehr. Diese Seite sagt dir, wo du sie findest. Gewisse Maschinen darfst du erst benutzen, nachdem du einen Kurs absolviert hast. So ist es auch mit der CNC-Fräse im Fab Lab Zürich.
Im Kurs lerne ich zunächst, wie ich im RhinoCAM Schneidwege erzeuge. CAM steht für Computer Aided Manufacturing. Im CAM-Plugin für Rhinoceros – dem CAD-Programm, das im Fab Lab verwendet wird – gebe ich der CNC-Fräse Informationen zu Rohmaterial und den Fräs-Bearbeitungsschritten.
Privat werde ich nicht mit RhinoCAM arbeiten. Ich setze auf Fusion 360 CAM, da es gratis ist. Dennoch erhalte ich im Kurs wichtige Informationen, worauf ich beim Arbeiten in einer CAM-Software achten muss.
Im Kurs beginnen wir mit dem Import eines Testteils. Nach dem Import ist es wichtig, die X-, Y- und Z-Achsen zu definieren. So kennt die Fräse die Ausrichtung des Modells. Anschliessend muss ich noch die Dimensionen des Stocks, des Rohmaterials, angeben. So weiss die Fräse, aus was für einem Objekt sie das Modell ausfräsen muss. Das war mir nicht bewusst, aber leuchtet mir jetzt ein. Die Fräse kann nicht wissen, was in meinem Kopf vorgeht und deshalb muss ich ihr alles Schritt für Schritt erklären.
Danach definiere ich die Fräs-Bearbeitungsschritte. Das Testteil wird in vier Schritten gefräst. Als erstes steht das Roughing, auf Deutsch «Schruppen», an. Danach folgen Finishing (Schlichten), Engraving (Gravieren) und Profiling (Ausschneiden). Beim Schruppen werden grob die Konturen des Modells ausgefräst. Beim Finishing werden diese verfeinert. Danach graviere ich das Fab-Lab-Logo und zu guter Letzt schneide ich das Modell aus dem Rohmaterial aus.
Für jeden Arbeitsschritt muss ich gewisse Einstellungen vornehmen. Als erstes definiere ich, welche Regionen oder Eigenschaften die Fräse bearbeiten soll. Danach lege ich fest, mit welchem Fräser der Arbeitsschritt ausgeführt werden soll. Dabei ist es wichtig, das Werkzeug exakt zu erfassen. Das wurde im Fab Lab glücklicherweise bereits erledigt. Zuhause muss ich all meine Fräser im CAM erfassen. Das klingt zwar mühsam, ich freue mich aber darauf. Nur so kann ich richtig arbeiten.
Danach muss ich noch Einstellungen zu Schnittparametern, Schnitttiefen, Geschwindigkeiten und vielem Weiterem vornehmen. Wichtig ist auch hier, dass ich alle Angaben korrekt erfasse. Je nach Material und gewünschtem Ergebnis können die Einstellungen variieren. Bei allen vier Arbeitsschritten nehme ich unterschiedliche Einstellungen vor. Mir wird immer bewusster, dass die Grenze zwischen Gelingen und Scheitern eines Fräs-Jobs sehr klein ist. Toll, ich liebe solche Herausforderungen und freue mich darauf, bei jedem künftigen Projekt wieder neue Hindernisse zu überwinden.
Danach stelle ich das File für den Postprozessor bereit. Der Postprozessor setzt meine Ergebnisse von RhinoCAM in ein CNC-Format um.
Nach all der theoretischen Arbeit darf ich endlich an die Maschine. Dazu fixiere ich mein Rohmaterial mit Spannmitteln auf der Opferplatte.
Danach stelle ich zuerst den Nullpunkt der X- und Y-Achsen über den CNC-Controller ein. Beim Nullpunkt der Z-Achse gehe ich gleich vor wie bei einem 3D-Drucker. Ich lege ein Papier auf mein Rohmaterial und senke den Fräser. Sobald ich das Papier nicht mehr bewegen kann, fixiere ich den Nullpunkt.
Danach starte ich den Fräs-Job und überwache ihn.
Beim Testteil wechsle ich zwei Mal das Werkzeug. Fürs Schruppen und Ausschneiden verwende ich einen Schaftfräser, fürs Schlichten und Gravieren einen Kugelkopffräser. Da ich die Arbeitsschritte im RhinoCAM eingegeben habe, pausiert die Maschine nach dem Schruppen und ich kann den Schaftfräser einspannen. Nach dem Schlichten und Gravieren montiere ich wieder den Kugelkopffräser fürs Ausschneiden.
Nach weniger als einer Viertelstunde ist mein Testteil bereits ausgefräst. Toll, so macht’s Spass. Das Ergebnis meiner üblichen Arbeit, also meine Online-Artikel, sehe ich zwar auch, aber etwas Festes in den Händen zu halten, ist noch geiler. Jetzt bin ich definitiv angefixt und bereit, mit meiner eigenen Fräse die nächsten Schritte anzugehen.
Eine CNC-Fräse ist etwas Tolles, aber sie ist dumm. Ich muss sie exakt mit vielen Daten füttern, damit sie weiss, was sie zu tun hat. Sonst passiert, was mir beim letzten Mal passiert ist: Mein Fräs-Auftrag misslingt.
Dank dem Kurs weiss ich jetzt besser Bescheid, welche Einstellungen für was sind. Jetzt muss lernen, was das im Detail für meine einzelnen Projekte bedeutet.
Selbstverständlich habe ich meine Kursleiter auch spezifisch für meine Projekte ausgefragt und Tipps erhalten. Ich übe mit Holz oder Polystyrol, bevor ich mich ans Acryl-Fräsen mache und nehme demnächst Modifikationen an meiner Fräse vor.
Zu meinem Schutz baue ich ein Gehäuse für meine Maschine. Ich habe bereits eine Idee, wie das aussehen soll. Zudem hat meine Fräse keine Endschalter. Die sind wichtig, damit die Maschine weiss, wo die Endpunkte der Achsen sind. Ohne Endschalter können die Schrittmotoren beschädigt werden.
Mein CNC-Abenteuer geht weiter. Beim nächsten Mal berichte ich dir von meinen Modifikationen und den ersten Fräsaufträgen.
Technologie und Gesellschaft faszinieren mich. Die beiden zu kombinieren und aus unterschiedlichen Blickwinkeln zu betrachten, ist meine Leidenschaft.